Plastics pros enhance skills at Penn College
Published 08.15.2023
A diverse group of plastics professionals from throughout North America experienced higher-level technology in rotational molding during a recent workshop hosted by Pennsylvania College of Technology and its renowned Plastics Innovation & Resource Center.
Twenty-one individuals from 13 companies learned the connection between material preparation, molding and final part quality at the Rotational Molding & Advanced Materials Workshop. The two-day session offered a mix of lecture and hands-on experience at the college’s Shell Polymers Rotational Molding Center of Excellence.
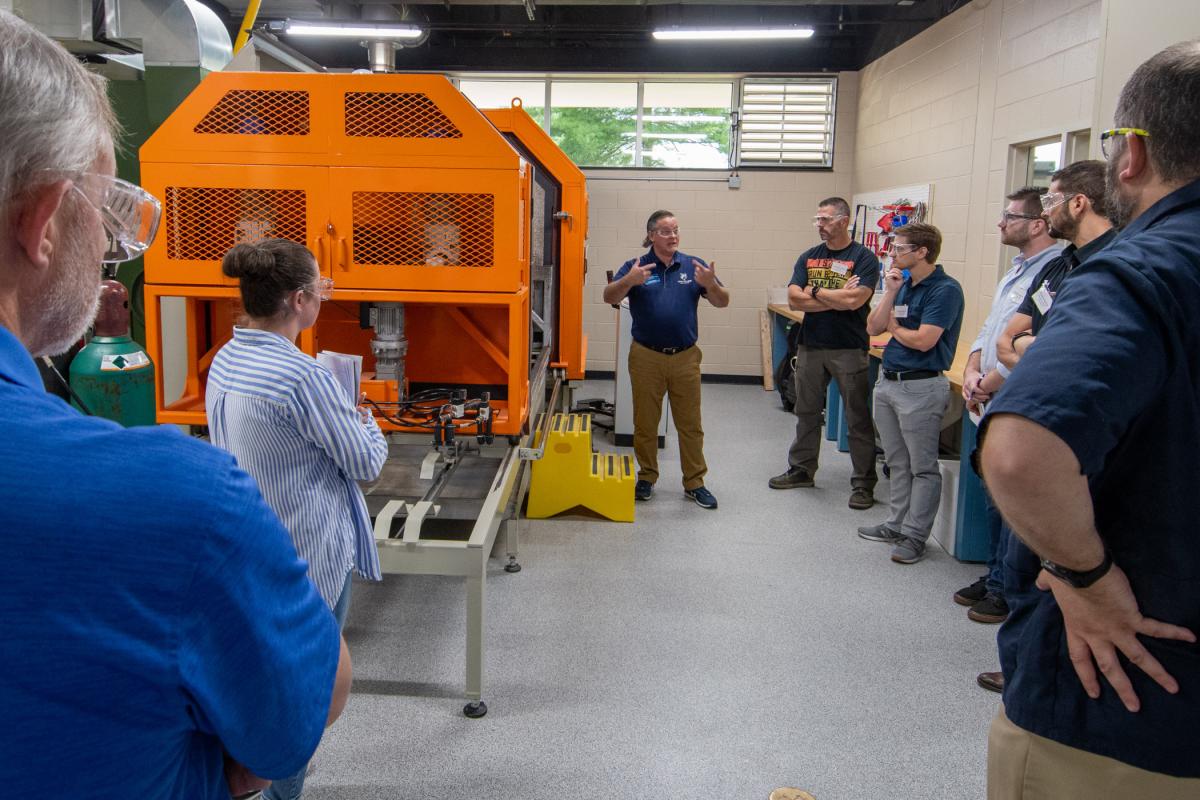
Dru Laws, an industry leader and operations expert, served as workshop presenter. Laws teaches at Brigham Young University-Idaho, serves as CEO of Halltech Systems in Rexburg, Idaho, and is a member of the Association of Rotational Molders’ Rotational Hall of Fame.
The workshop earned rave reviews from the participants, representing nine states and Canada.
“This workshop provides a great opportunity to interact with individuals from across the industry, broadening your knowledge base outside the four walls of your own facility. It also gives the chance to be exposed to some of the best technology in the rotomolding world, inspiring innovative ideas to travel back to facilities over the globe,” said Weston Johnson, process engineer at Dometic in Sparta, Tennessee.
“I enjoyed the hands-0n training and the in-depth explanations of the processes. I feel I can bring back what I’ve learned to my company to improve processes and quality,” said Miranda Barnhart, production supervisor at Senneca Holdings in Redmond, Oregon.
“Classroom time with a rotomolding expert helped deepen my understanding of principles of rotomolding, which will allow me to better train technicians and increase throughput and consistency,” added Andrew Eisterhold, laboratory technologist at ExxonMobil in Baytown, Texas.
“It was amazing,” summed up Martin Reimer, production technician at Vista Plastic Solutions in Winkler, Manitoba, Canada.
Penn College workshop facilitators were Christopher J. Gagliano, PIRC project manager; Nathan A. Rader-Edkin, PIRC program manager; and Jose M. Perez, instructor of plastics and polymer technology.
M. Holland Co. in Northbrook, Illinois, served as platinum sponsor.
The PIRC is one of the top plastics technology centers in the nation for research, development and education related to injection molding, extrusion, blow molding, rotational molding and thermoforming. To learn more, call 570-321-5533.
Penn College is one of seven institutions nationwide offering plastics degrees that are accredited by the Engineering Technology Accreditation Commission of ABET. Students may seek a bachelor’s degree in plastics & polymer engineering technology or an associate degree in plastics & polymer technology.
For information about those and other majors within the School of Engineering Technologies, call 570-327-4520.
Penn College is a national leader in applied technology education. Email the Admissions Office or call toll-free 800-367-9222.